Maximizing Efficiency and Quality with Volumetric Concrete Plants
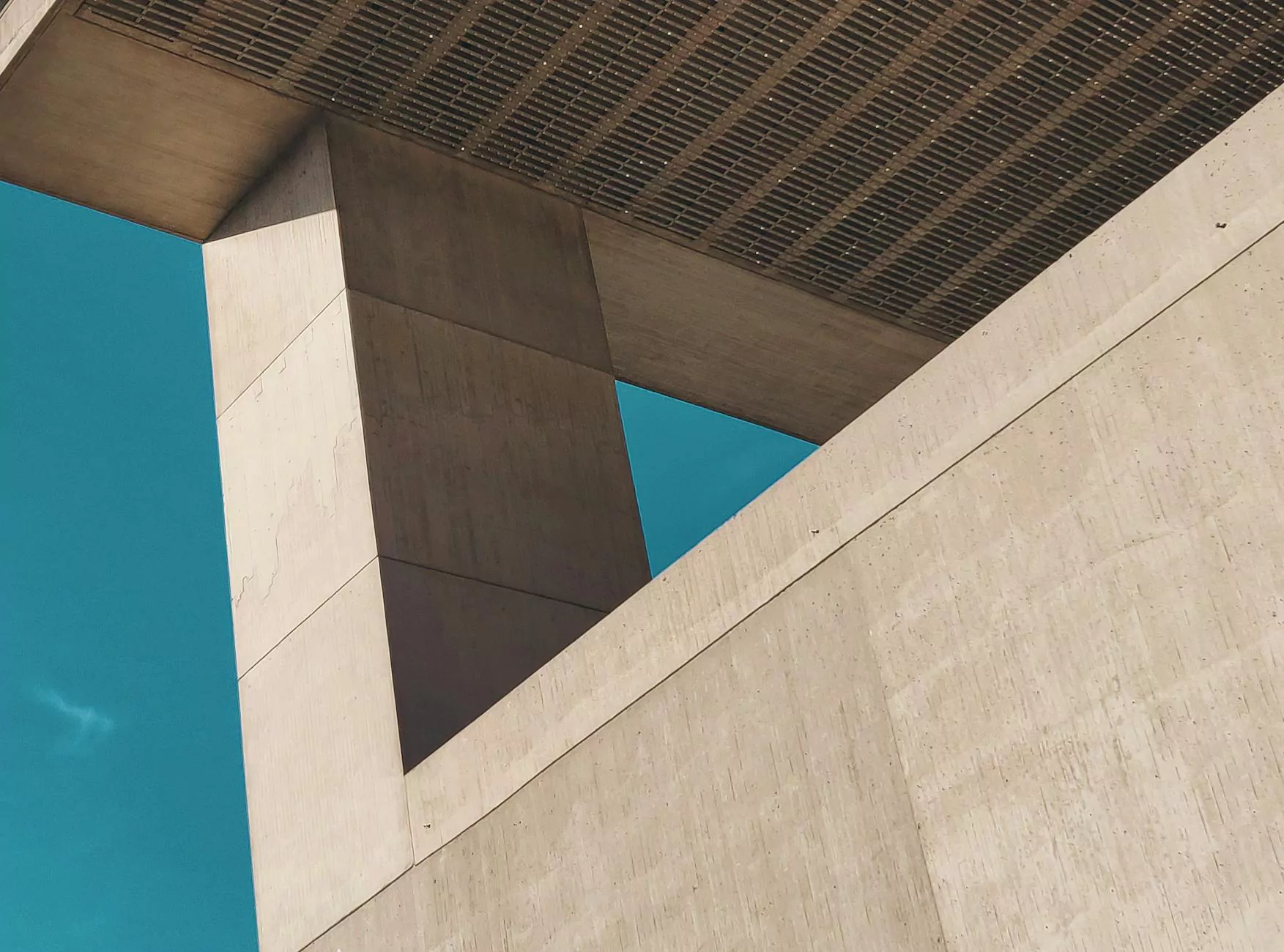
In an ever-evolving landscape of construction and manufacturing, businesses are continuously seeking ways to enhance their operational efficiency and product quality. One of the pivotal innovations making waves in the industry is the volumetric concrete plant. This article delves deeply into the intricacies of volumetric concrete plants, their benefits, their workings, and why they are crucial for modern construction and manufacturing processes.
Understanding Volumetric Concrete Plants
A volumetric concrete plant, also known as a mobile concrete plant, is an innovative solution for mixing concrete and delivering it on-site. Unlike traditional batch plants, which prepare concrete beforehand and require transportation, volumetric plants mix concrete on demand. This ensures that the product remains fresh, which is critical for maintaining quality standards in construction.
Key Components of a Volumetric Concrete Plant
To fully appreciate the advantages of a volumetric concrete plant, it's essential to understand its core components:
- Cement Silos: These store bulk cement and allow for easy access during the mixing process.
- Aggregate Bins: Typically part of the setup, these bins store different aggregate materials such as sand, gravel, or crushed stone.
- Water Tank: A substantial source of water is necessary for the mixing process, and the plant’s water tank facilitates this efficiently.
- Mixer: This device mixes the aggregates, cement, and water in the right proportions to create concrete. Unlike traditional mixers, it can adjust the mix ratio as needed.
- Control System: The heart of the plant, where operators can manage and precisely control the mixing process and ensure quality compliance. This often includes advanced digital solutions for monitoring output and consistency.
The Working Principle of Volumetric Concrete Plants
The operation of a volumetric concrete plant is straightforward yet sophisticated, combining technology and material science. Here’s a step-by-step breakdown of how they work:
- Material Loading: Operators load the required amount of aggregates and cement into their respective bins.
- Water Measurement: Based on the required amount of concrete, the control system calculates the precise water needed.
- Mixing: The mixer then combines the materials, starting the mixing sequences as the operator monitors the process.
- Delivery: Once the concrete reaches the desired consistency, it is discharged through a delivery system, ready for immediate use on-site.
Benefits of Using Volumetric Concrete Plants
Transitioning to a volumetric concrete plant provides several significant advantages that can drastically improve construction project outcomes:
1. Freshness and Quality Control
One of the standout benefits of volumetric mixing is the ability to produce fresh concrete on-site. Traditional methods often involve transportation issues and time delays, which can compromise the quality of the concrete. With a volumetric concrete plant, businesses can guarantee that their concrete is mixed to order, reducing waste and ensuring that every batch meets quality specifications.
2. Cost Efficiency
Investing in a volumetric concrete plant can lead to significant cost savings. The on-demand mixing reduces the need for surplus concrete and minimizes transportation costs associated with traditional methods. As a result, businesses can allocate resources more effectively, lowering overall project costs.
3. Flexibility and Customization
Different projects have varying concrete requirements. Volumetric concrete plants allow operators the flexibility to customize mixtures based on real-time needs. Whether it’s adding fibers for reinforcement or adjusting the slump according to application requirements, the customization possibilities are vast.
4. Space and Environmental Considerations
Unlike traditional batch plants requiring extensive space for storage and mixing, a volumetric concrete plant is typically compact and mobile. This versatility enables businesses to set up in various locations—ideal for urban construction sites with limited space. Furthermore, since materials are mixed as needed, the environmental footprint of surplus concrete disposal is greatly reduced, aligning with sustainable construction practices.
5. Streamlined Operations
With advanced automation and control systems, volumetric concrete plants streamline operations significantly. This automation allows for quicker setup times and lower labor costs, as fewer workers are needed to manage multiple stages of production.
The Role of Technology in Volumetric Concrete Plants
Modern volumetric concrete plants are equipped with cutting-edge technology that enhances functionality and efficiency. Key technological advancements include:
- Digital Control Systems: Allow for real-time monitoring and adjustments during mixing, ensuring consistent quality.
- Automated Sensors: These sensors track material levels and monitor the mixing process automatically, reducing manual errors.
- Telematics: Advanced tracking systems provide data about the mixer’s performance, helping operators to optimize usage and maintenance schedules.
- Remote Access: Some systems allow for remote handling, enabling operators to manage the plant from a distance.
Applications of Volumetric Concrete Plants
The versatility of volumetric concrete plants means they are applicable in a wide array of projects. Here are a few key areas where they excel:
1. Residential Construction
Home builders often rely on volumetric concrete for foundations, driveways, and walkways, enabling them to deliver the required concrete precisely when it's needed, enhancing project flow and efficiency.
2. Commercial Projects
From office buildings to retail spaces, volumetric concrete plants offer the flexibility to manage various concrete requirements that commercial projects demand, allowing for rapid deliveries and custom mixes.
3. Infrastructure Development
Road construction, bridges, and public works projects greatly benefit from the speed and quality control of volumetric concrete plants, ensuring that projects are completed on time and within budget.
4. Specialized Concrete Applications
For projects requiring unique concrete formulations, volumetric plants provide the technological adaptability needed to produce materials such as high-strength concrete or those infused with additives for specific environmental conditions.
Choosing the Right Volumetric Concrete Plant Manufacturer
When investing in a volumetric concrete plant, it is essential to select a reputable manufacturer. This decision can greatly affect your project’s success. Here are some factors to consider:
- Experience and Reputation: Look for a manufacturer with a proven track record in the industry and positive customer feedback.
- Technology Integration: Ensure that they offer modern, efficient systems that incorporate the latest technological advancements.
- Support and Service: Evaluate the after-sales support available, such as training, maintenance, and emergency assistance.
- Customization Options: A good supplier should be able to cater to your specific needs, offering plants that can be customized for different projects.
The Future of Volumetric Concrete Plants
As the construction industry continues to evolve, the role of volumetric concrete plants is expected to grow. Innovations in design and function will further enhance their capabilities, making them indispensable for efficient and sustainable construction practices. The rise of smart technology and automated processes is set to revolutionize the way concrete is mixed and delivered, leading to even greater efficiencies and quality assurance.
Conclusion
In conclusion, adopting a volumetric concrete plant represents a significant step forward for any construction or manufacturing business looking to improve efficiency and product quality. With their numerous advantages ranging from freshness and cost savings to operational flexibility and technological advancements, volumetric concrete plants are more than just an option—they are a necessity.
As industry leaders like Polygon Mach continue to innovate within the realms of Electronics and 3D Printing, embracing volumetric concrete mixing technology will drive success and elevate project delivery standards. For businesses aiming to thrive in today’s competitive environment, investing in a volumetric concrete plant is an investment in their future.